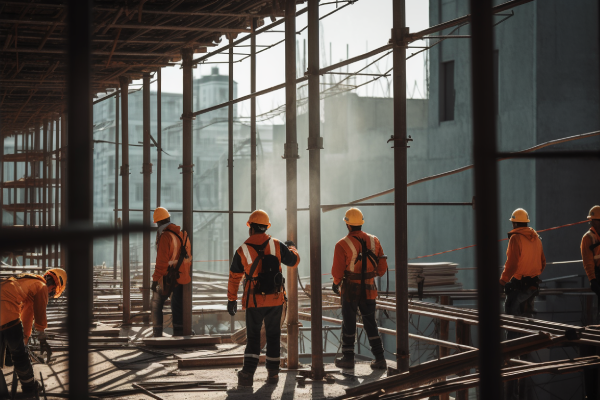
The 10 essential PPE for your safety
Safety in the workplace is a top priority, not only to protect the health and well-being of employees but also to maintain optimal productivity. In this world where professional risks are as diverse as they are varied, Protective Equipment Individual (PPE) play a crucial role. This article aims to shed light on good practices regarding PPE, essential for any worker concerned about their safety.
Summary
What is PPE?
Personal Protective Equipment (PPE) is crucial for protecting workers against risks threatening their health and safety at work. They serve as a protective barrier when risks cannot be eliminated or reduced by other preventive or organizational means.
Definition of PPE
Personal Protective Equipment (PPE) are devices designed to protect workers against various risks threatening their health or safety. Governed by international and local standards, they must meet strict performance and safety criteria, such as CE marking in Europe which ensures their compliance with Regulation (EU) 2016/425. These standards ensure that PPE provides an effective barrier against hazards, playing a crucial role in the prevention of accidents and occupational illnesses.
The different types of risks covered by PPE
PPE provides protection against a variety of hazards, such as chemical, thermal, biological, electrical, and mechanical hazards.Each type of hazard requires specific equipment, designed to provide protection as efficient as possible.
The 10 essential PPE
- Worksite helmets: Protection against falling objects. Essential on construction sites, they protect the head from impacts and potential injuries. The use of hard hats is mandatory on most construction sites to minimize the risk of head trauma.
- Protective glasses: Eye safety against projections. They prevent eye damage from flying particles, chemical splashes or dangerous radiation. The choice of glasses must be adapted to the specific working environment.
- Work gloves: Hand protection against cuts, burns and chemicals. They are essential for safely handling potentially hazardous materials or substances. A wide range of work gloves are available to meet different risk levels.
- Safety shoes: Protection of the feet against crushing and punctures. They also provide additional grip to prevent falls. Some models are equipped with anti-perforation soles and protective shells.
- Hearing protection: Prevention against hearing damage in noisy environments. Earplugs or headphones are crucial to preserving hearing. Their use is recommended or mandatory in areas where noise levels exceed regulatory limits.
- Respiratory protection: Air filtration in contaminated or dusty areas. Masks and respirators protect against the inhalation of harmful substances. They are essential in industries where workers are exposed to fine dust, fumes or toxic vapors.
- Fall protection: Safety for working at height. Harnesses and lifelines are vital to preventing falls from height. These safety systems are essential for work on scaffolding, roofs, or in any environment where the risk of falling is present.
- High visibility clothing: Ensure worker visibility in low light areas or on roads. These high-visibility clothing help prevent accidents by making workers more visible, especially during low light conditions or at night.
- Protective suits: Protection against chemicals or hazardous materials. They provide a safety barrier against dangerous exposures. These suits are designed to resist a wide range of chemicals and provide a level of protection appropriate to exposure.
- Protection equipment against falls from height: Fall arrest systems for work at height. Essential for high-risk work, they prevent serious or fatal injuries. The installation of these systems must be carried out by professionals and regularly inspected to ensure their effectiveness.
Employer obligations
Employers must provide free of charge PPE adapted to the risks of the workplace, following a thorough hazard assessment. They are also required to keep this equipment in good condition, through regular maintenance, and to train employees on its correct use and the risks linked to their activity. This training must include information on how to check the condition of PPE and the procedures to follow for its maintenance or replacement.
Employee obligations
Employees, for their part, must use PPE in accordance with the training and instructions provided by the employer. They are responsible for the routine maintenance of PPE and must immediately report any failure or wear, thus ensuring their protection and that of their colleagues.
PPE selection and testing
The selection of PPE requires a precise assessment of the risks linked to each professional activity, allowing the most suitable equipment to be chosen. Before being put into service, it is crucial to test PPE in real conditions of use to ensure their effectiveness and comfort, thus guaranteeing the best possible protection for users.< /p>
Training and awareness
Training and raising awareness of employees on the correct use of PPE and compliance with safety instructions are key steps for effective protection.Employers should organize regular training sessionsand adapt content to the specificities of positions and changes in safety standards, while leading awareness campaigns to promote a safety culture within the company.
In short, rigorous PPE management relies on close collaboration between employers and employees, careful selection of equipment based on risk assessment, and a continuous commitment to training and safety awareness.